ViscoScope® from MARIMEX®
Measure viscosity in the process

With ViscoScope®, we have developed a maintenance-free inline measuring system
that allows you to monitor viscosity precisely, reliably, and in real time directly in the process.
Maintenance-free viscosity measurement that accelerates your process
With our ViscoScope viscosity sensor, you take no risks. The maintenance-free measuring device, calibrated with special shear-independent calibration oils, can be used after installation to measure viscosity in your process. Your production runs with the highest process reliability at all times. For batch and continuous processes in almost all industrial applications.
Viscosity determination with the inline measuring system from MARIMEX®
- Durability thanks to robust stainless steel housing
- Sensor completely welded
- Various installation positions can be realized in your process
- precise & reproducible measurement results
- Approval for Ex and non-Ex areas
- Available as a measuring system or stand-alone solution
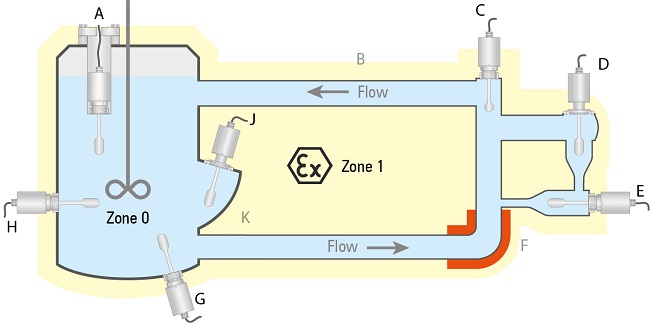
Download further information on possible installation positions here: installation positions
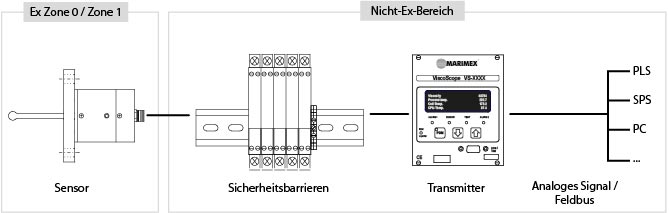
Do you need an Ex version? All ViscoScope inline process viscometers are equipped with ATEX / IECEx and CSA certificate
- HART protocol
- Profibus
- Analog signal
- ModbusRTU
Inline integration of process viscometers
Various output signals allow you to integrate the device into existing process control systems.
MARIMEX viscosity sensors can be easily integrated into your new and existing systems. Even if your production is restructured for process-related reasons, the viscometer can continue to be used.
With our accessories you can measure the dynamic viscosity directly in the process in almost any application (inline viscosity measurement).
With our viscosity sensor you increase your process quality and avoid faulty batches
Measuring viscosity is an excellent way to achieve higher quality in the process.
Inconsistent product quality and defective batches can often be traced back to unnoticed changes in process conditions. MARIMEX® viscometers help you maximize your yield and avoid production-related revenue losses.. With our viscosity measuring device, the ViscoScope® from MARIMEX®, you can measure viscosity in real time directly in your process. Use the newly acquired knowledge to optimize and control your manufacturing process
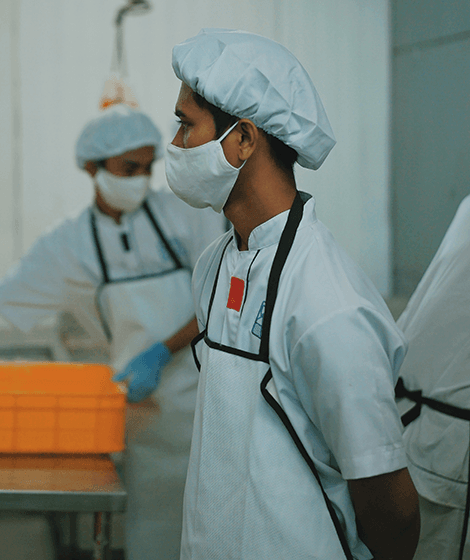
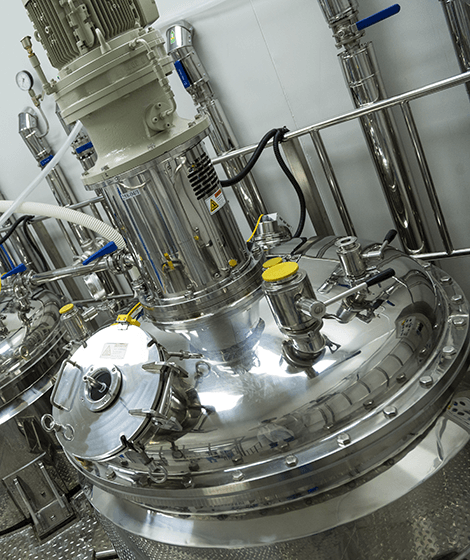
Inline viscosity measurement maximizes your yield & saves costs
Through precise and reliable process knowledge of the viscosity parameter, you can achieve higher quality in your process.
Our inline viscosity measuring device supports you as a user in achieving optimal process control. With our process viscometer, you use only as much raw material and energy in your process as you actually need to achieve the desired end product. You can use the measurement results, for example, to control dosing quantities and mixing ratios or to regulate the temperature of your manufactured product.
Rely on the quality parameter viscosity & trust ViscoScope® from MARIMEX®.
Work with our application engineers to find out how you can use viscosity measurement in your specific application to improve process quality. We have already successfully installed our measurement system for a large international customer base.
Petrochemicals
MARIMEX® Viskositätsmessung
Petrochemical industry
- Asphalt and bitumen mixtures
- Control of the oil bunkering process
- Flow measurement in pipelines
- Flowability of lubricants
Food
MARIMEX® Viskositätsmessung
Food industry
- Addition of thickeners
- Addition of raw materials in baked goods
- Adding water to frozen goods
- Drying of animal feed products
Pharmaceuticals & Cosmetics
MARIMEX® Viskositätsmessung
Industry & Pharmacy
- Shape stability of creams & lotions
- Final viscosity of herbal extractions
- Filling of shampoo and toothpaste
- Strength of gelatin capsules
Chemical
MARIMEX® Viskositätsmessung
Chemical industry
- Dosing of paints and varnishes
- Application of paper coatings
- Production of polymer melts
- Solvent addition to adhesives and sealants
- Rheometer
- Viscometry
- Rheometry
- Viscometer
Inline viscometers bring the test laboratory to the machine
Get laboratory-quality viscosity measurements.
Our viscosity measurement system allows you to permanently record important process conditions at the site, which you can use for process control, documentation and monitoring purposes.
Save a lot of time and bring the lab to your machine. This will reduce the number of submissions to laboratories and other testing facilities.
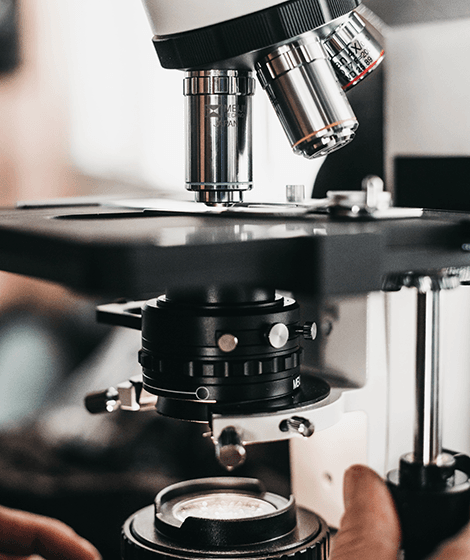
Inline Viscosity Meter: Frequently Asked Questions
ViscoScope® from MARIMEX®
Due to the low amplitude at the system's resonant frequency, the sensor is not subject to material fatigue or deterioration. Since the probe is completely welded, there are no moving parts, bearings, or seals on the sensor. We have numerous applications where the systems have been running 24/7 for more than 10 years. A calibration check of the viscometer is not required. However, quality management regulations often require an annual calibration check. Please contact us if you would like a system check.
Marimex is the optimal partner for your process
We support you from application-specific consulting to the customer-specific device. We provide expert support during the installation of your measuring device. We provide on-site training for you and your staff in the use of the measuring system and the interpretation of the measured values.
Application consulting
Together with our application engineers, you will find a useful application that will sustainably improve your process quality.
Commissioning support
After consultation and ordering, we will support you until the measuring device is working optimally at its intended location.
User training
We train you and your employees on-site and show you how to interpret and use your measured values.
German Producer - Global Supplier
Our know-how in viscosity measurement is your competitive advantage
- We are specialists in inline viscosity measurement with 25 years of experience
- Our engineers support you in planning, installation and interpretation of the measured values
- "Made in Germany" - We produce in Germany and deliver worldwide
- We have distributors in many industrialized nations worldwide
Your benefits at a glance
- You gain new insights into your manufacturing or production process
- You avoid faulty production and faulty batches
- You increase the quality and process reliability in your production with sensor support
- You monitor the quality parameter viscosity permanently and directly in the process
- You use a modern, maintenance-free measuring system with very high measuring accuracy and reproducibility
Nehmen Sie Kontakt mit uns.
Unsere erfahrenen Vertriebsingenieure freuen sich auf Ihre Anfrage!
Vertrieb International
info@fluidio.de +49-6251-8462-0